Which one to choose between semi-automatic and automated packaging lines?
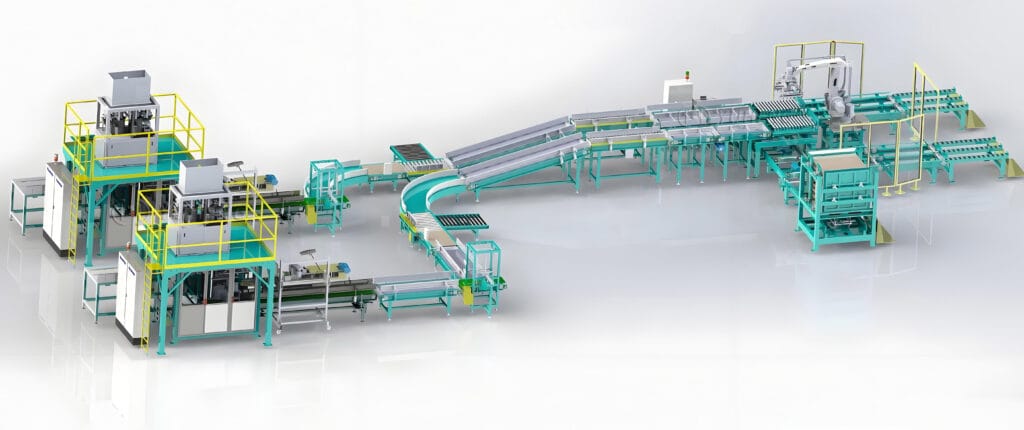
Yuheng Smart Packaging Solutions Guide: 21 Key Factors for Choosing Between Semi vs Full Automation
H1: Automation Level Decision Matrix 2025: Data-Driven Selection Guide by Yuheng Industrial Experts
![Yuheng modular packaging system with collaborative robots]
Alt: Yuheng’s intelligent packaging workstation handling fragile items with pneumatic grippers – ISO 9001 certified production line
Understanding Automation Levels: A Quick Start Guide
Basic Definitions (ASTM Standards):
Full Automation: Systems requiring <5% human intervention (material loading to final palletizing)
Semi-Automation: Human-machine collaboration with 30-70% manual operations
Manual Systems: >80% human-dependent processes (not covered in this guide)
The 5D Decision Framework
Developed through analysis of 1,200+ global implementations, Yuheng’s selection model evaluates:
Throughput Demand
Units per hour (UPH) requirements
Shift patterns (single vs 24/7 operations)
Product Complexity
Fragility level (e.g., glass vs plastic)
Size variation (fixed vs mixed dimensions)
Capital Efficiency
Initial investment vs long-term ROI
Government incentives (e.g., EU automation subsidies)
Workforce Strategy
Skill availability (technicians vs general labor)
Training infrastructure
Scalability Needs
Future expansion plans
Technology upgrade pathways
Head-to-Head Comparison
Fully Automated Systems: Yuheng AutoPack Pro 5.0
Technical Specifications:
Speed: 200-300 packs/minute (adjustable via HMI)
Accuracy: ±0.1mm laser-guided positioning
Energy Use: 0.7kW·h/1000 units (ENERGY STAR certified)
When to Choose:
✅ High-volume production (>1M units/month)
✅ Strict hygiene requirements (pharma/food)
✅ Hazardous material handling
Real-World Case:
German dairy producer achieved:
92% labor cost reduction
40% faster time-to-market
Zero recall incidents in 3 years
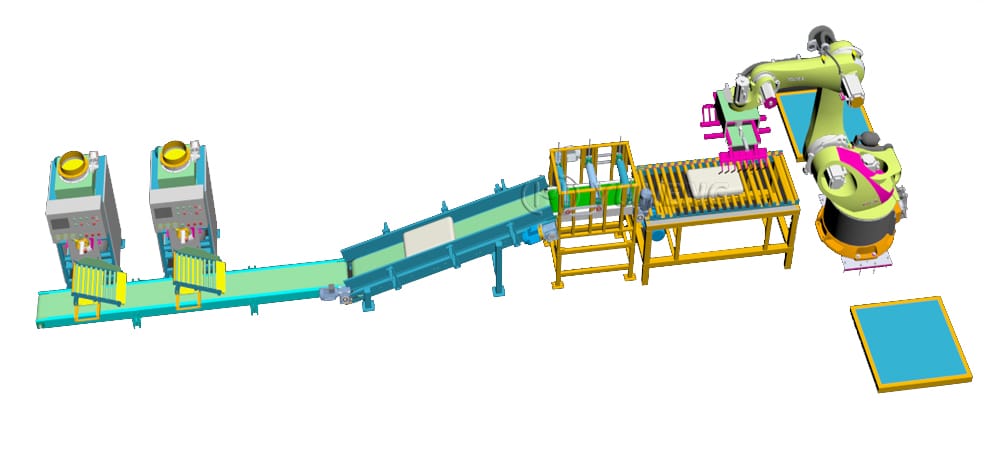
Semi-Automated Systems: Yuheng FlexiPack Hybrid 3.0
Innovation Highlights:
Safety System: 3D vision barrier (CE EN ISO 13855 compliant)
Quick Changeover: <15 minutes for SKU switching
Ergonomic Design: Height-adjustable workstations
Economic Analysis (USD):
Cost Factor Full Auto Semi Auto
Initial Cost $850,000 $280,000
Annual Labor $45,000 $120,000
Maintenance $65,000 $35,000
5-Year TCO $1.1M $635K
Industry-Specific Recommendations
Food & Beverage Sector
Best Practice:
Full automation for primary packaging
Semi-auto for final case packing
Yuheng Solution:
CIP (Clean-in-Place) compatible systems
USDA/FDA compliant material surfaces
Pharmaceutical Industry
Regulatory Must-Haves:
21 CFR Part 11 compliance
Electronic batch records
Yuheng Advantage:
Isolator technology for sterile environments
Blockchain-enabled traceability
Implementation Roadmap
Phase 1: Assessment
Conduct time-motion study
Map current workflow pain points
Phase 2: Prototyping
3D digital twin simulation
Virtual reality walkthrough
Phase 3: Deployment
Modular installation (minimal downtime)
Staff certification program
Phase 4: Optimization
Real-time OEE monitoring
AI-driven process improvement
Common Misconceptions Debunked
Myth 1: “Automation eliminates all jobs”
Reality: Yuheng’s clients report:
65% workforce upskilling
30% new technical roles created
Myth 2: “Semi-auto means lower quality”
Data: Properly implemented hybrid systems:
Achieve 99.2% first-pass yield
Allow 50% faster defect detection
If you want to know more about the equipment configuration and other details, please feel free to communicate with us