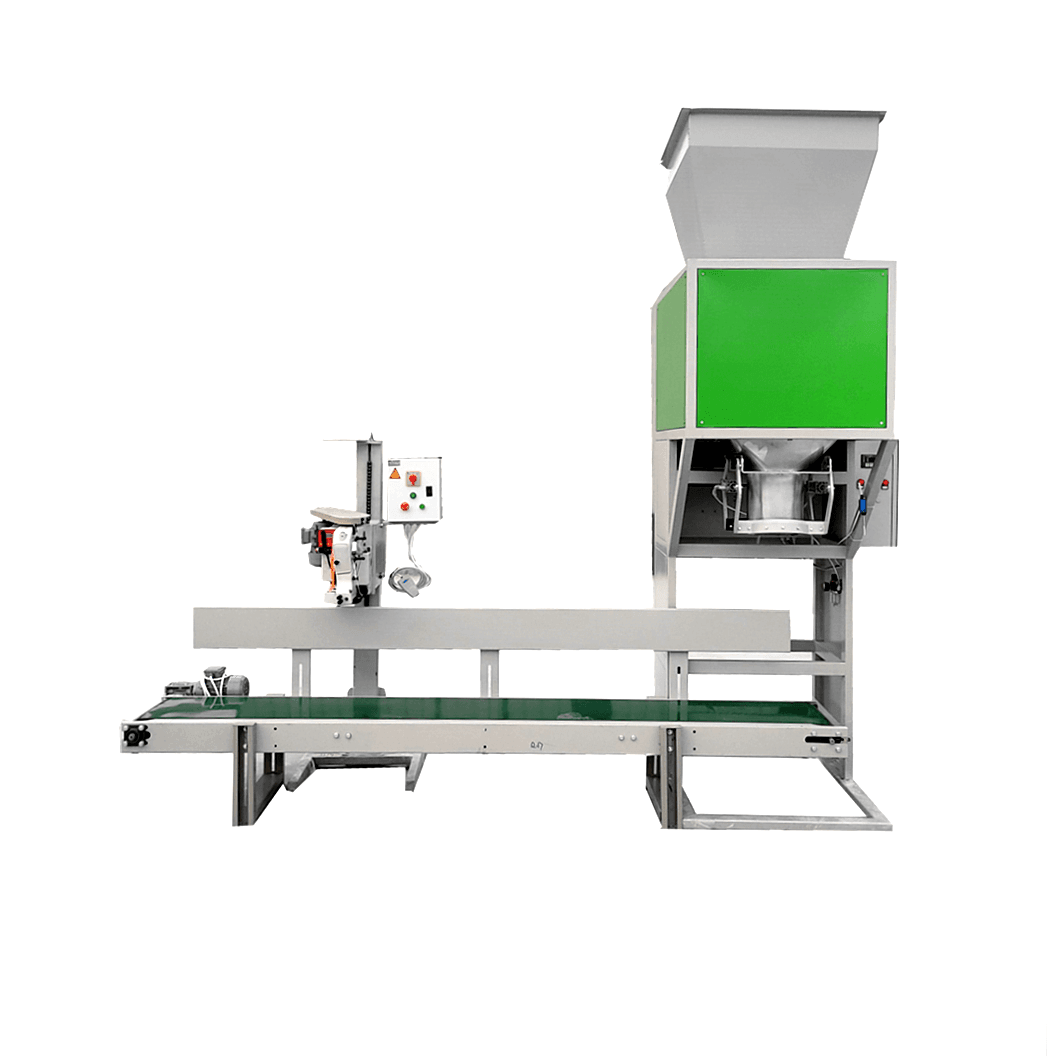
What Is the Price of Powder Packaging Machinery? Quick Solutions to Common Operational Issues
Powder packaging machinery plays a critical role in industries ranging from food production to pharmaceuticals, offering precision and efficiency for fine material handling. As a leader in this field, YU-HENG Technology combines China’s cost-effective manufacturing expertise with globally compliant engineering to deliver reliable solutions. Below, we address pricing considerations and practical troubleshooting strategies while highlighting the advantages of Chinese innovation and YU-HENG’s technical prowess.
Powder Packaging Machinery Pricing Overview
YU-HENG Technology provides tiered solutions to meet diverse production needs:
- Semi-automatic models: Starting from approximately $3,000
- Mid-range automated systems: $60,000–$130,000
- High-speed GMP-compliant lines: $180,000+
Chinese-manufactured equipment typically offers 30–40% cost savings compared to European or North American alternatives, with no compromise on ISO 9001-certified quality.
5 Common Operational Issues & Rapid Resolution Strategies
1. Material Clogging
Symptoms: Irregular flow, machine jams, or complete stoppage
YU-HENG Solutions:
- Patented Anti-Bridging Design: Reduces clogs in hoppers and augers
- Quick-Clean Access Panels: Enable debris removal in <10 minutes
- Compressed Air Ports: Integrated blast cleaning for stubborn residues
China’s Advantage: Durable 316L stainless steel construction resists material adhesion, extending service intervals by 50%.
2. Conveyance System Failures
Common Issues: Belt slippage, chain misalignment, or motor stalling
Troubleshooting Steps:
- Inspect tension on 1–2″ (25–50 mm) wide conveyor belts
- Lubricate roller bearings every 300 operating hours
- Replace worn sprockets using YU-HENG’s tool-free modular components
YU-HENG Innovation: SmartLoad™ sensors auto-adjust feed rates, preventing overloads that cause 80% of conveyor issues.
3. Dosing Inaccuracies
Root Causes: Humidity fluctuations, powder compaction, or sensor drift
Precision Recovery:
- Recalibrate auger fillers using test weights (5–50 lb / 2.3–22.7 kg)
- Activate vibration-assisted flow aids for cohesive powders
- Utilize YU-HENG’s CloudCal™ software for real-time adjustment logging
Performance Benchmark: Maintains ±0.35 oz (10 g) accuracy even with challenging materials like titanium dioxide or talc.
4. Weak Seal Integrity
Warning Signs: Leaks during transport, package inflation, or spoilage
Optimization Methods:
- Adjust heat jaws between 300–450°F (149–232°C) based on film thickness
- Test seal strength at 2–5 PSI (14–34 kPa) air pressure
- Replace worn Teflon® strips every 6–8 months
YU-HENG Advantage: Dual-seal technology with laser-aligned jaws ensures 99.9% leak-free performance, validated by third-party labs.
5. Mechanical Breakdowns
Typical Faults: Electrical shorts, gearbox noise, or PLC errors
Rapid Response Protocol:
- Reset main circuit breakers (200–480V compatible)
- Check lubrication levels in reduction gearboxes
- Review error codes via 10″ HMI touchscreen
- Contact YU-HENG’s 24/7 global support team
Preventive Maintenance:
- Annual motor inspections (5–15 HP / 3.7–11 kW models)
- Quarterly greasing of cam followers and linear guides
- Monthly air filter replacements in dusty environments
Why Choose YU-HENG Technology?
- Cost Efficiency: Localized production cuts lead times by 6–8 weeks
- Smart Diagnostics: IoT-enabled machines predict 70% of faults before failure
- Hygienic Design: CIP-ready systems meet FDA 21 CFR Part 11 standards
- Global Support: 18-month warranty with on-site training in 50+ countries