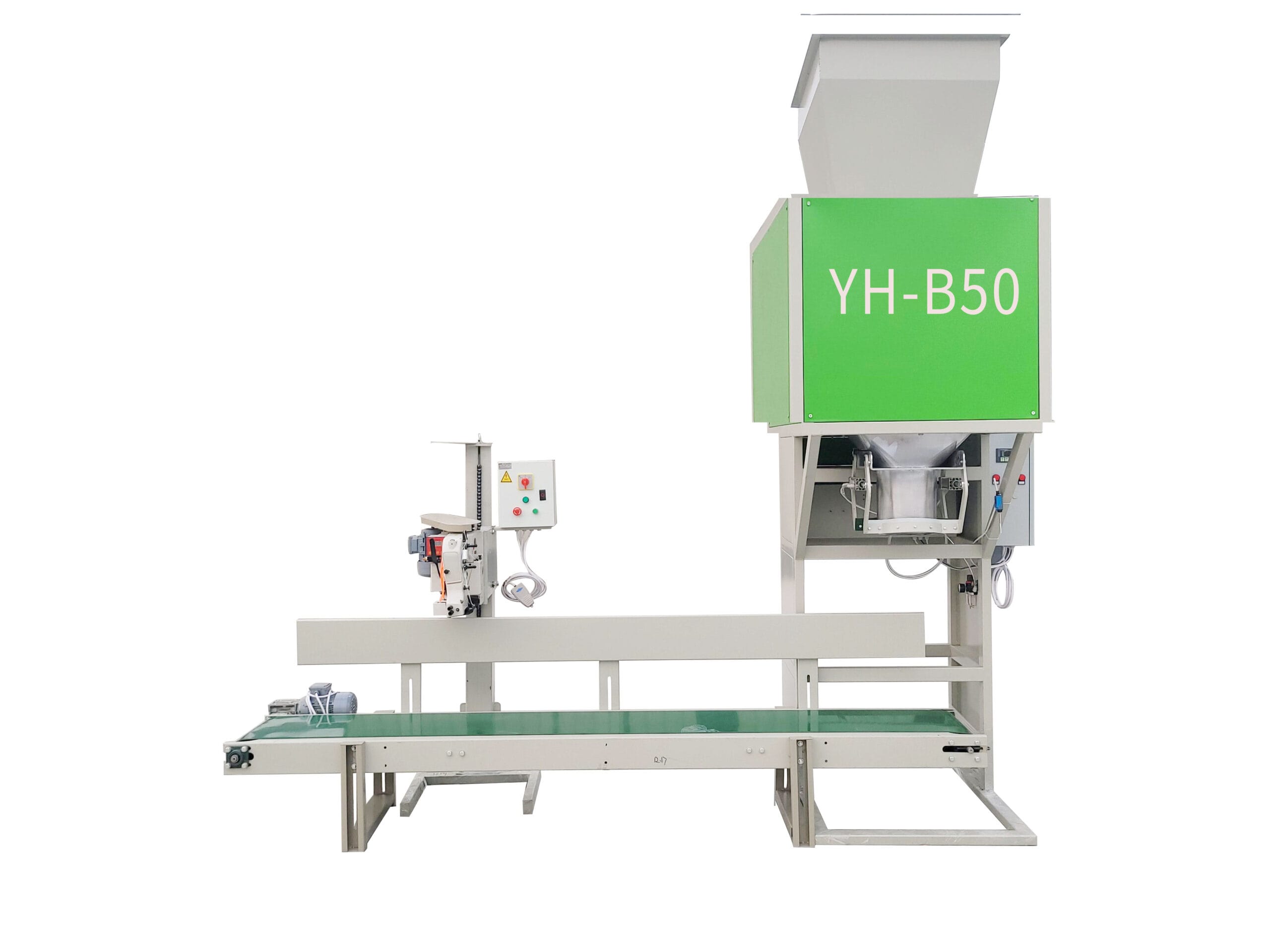
Powder Packaging Machine Costs & Comprehensive Management Strategies
Powder packaging machines are critical for industries handling materials like pharmaceuticals, food additives, and industrial chemicals. Effective management ensures peak performance and longevity. Below, we analyze pricing factors and outline actionable management practices, emphasizing cost-efficiency and operational reliability.
Powder Packaging Machine Pricing Overview
Equipment costs vary by automation and precision:
- Semi-automatic models: $5,000–$60,000 (20–50 bags/hour)
- Mid-range automated systems: $70,000–$150,000 (60–120 bags/hour)
- GMP-compliant lines: $180,000+ (nitrogen-flushed, IoT-enabled)
Chinese manufacturers offer 25–40% cost savings versus European brands while maintaining ISO 9001 compliance.
6 Key Management Practices for Optimal Performance
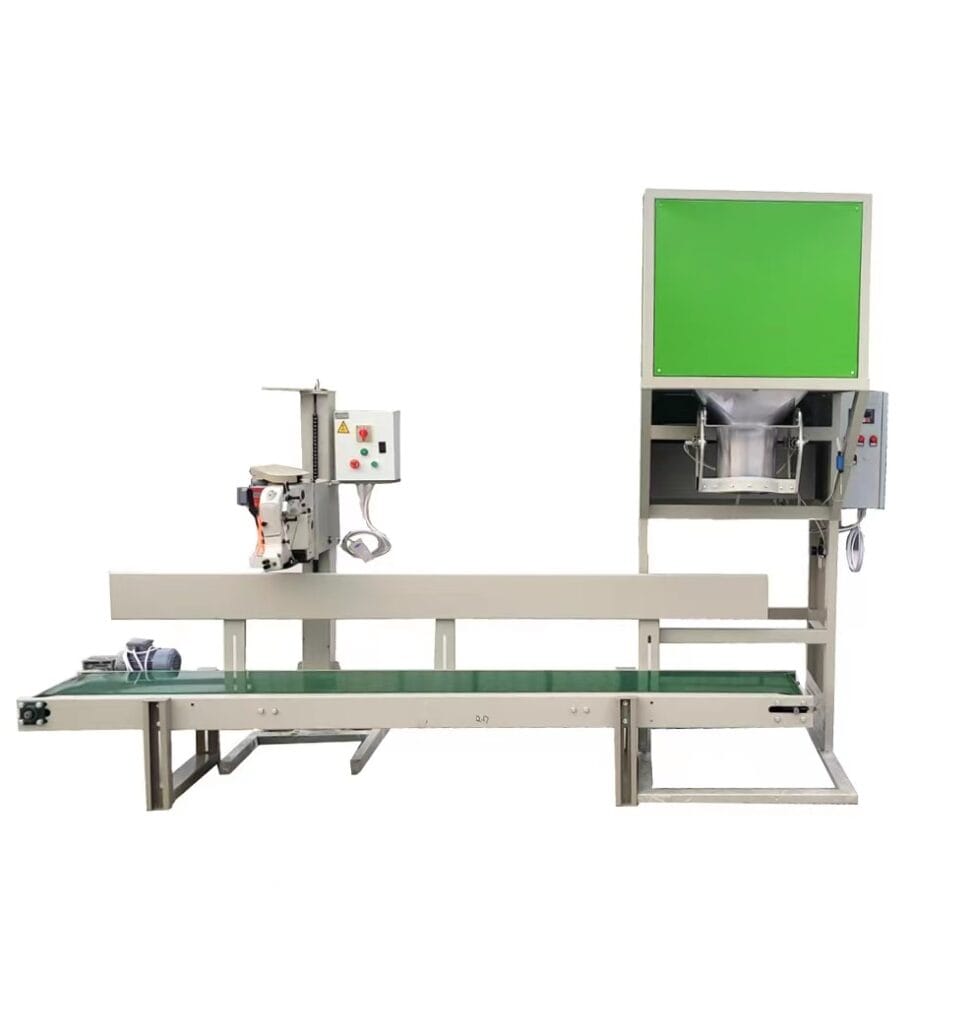
1. Institutionalized Management Frameworks
- Documentation: Develop SOPs for roles, maintenance schedules, and safety protocols.
- Accountability: Assign clear responsibilities for operators, technicians, and supervisors.
Example: A Midwest chemical plant reduced downtime 30% by implementing shift handover checklists.
2. Pre-Purchase Due Diligence
- Supplier vetting: Prioritize vendors with 5+ years of industry-specific experience.
- Factory acceptance testing (FAT): Verify performance metrics (e.g., ±0.5% dosing accuracy) before installation.
3. Operational & Maintenance Protocols
- Daily checks: Inspect seals, filters, and sensors.
- Lubrication schedule:
Component Lubricant Frequency
Auger drive Food-grade grease Every 200 hours
Conveyor bearings Synthetic oil ISO VG 68 Monthly Pro Tip: Use IoT-enabled tools to automate lubrication reminders. 4. Predictive Maintenance- Vibration analysis: Detect motor imbalances before failure.Thermal imaging: Identify overheating circuits or bearings.Cost impact: Reduces unplanned downtime by 50–70%.
- Core modules:Emergency shutdown procedures (<0.5 second response).Cross-contamination prevention for multi-product lines.Basic troubleshooting (e.g., clearing material jams).
- 6. Digital Monitoring Systems
- Real-time dashboards: Track OEE (Overall Equipment Effectiveness), energy use, and defect rates.
- Data analytics: Predict wear patterns for augers and seals using historical performance data.
- Preventive maintenance $5,000–$25,000 Partner with suppliers for discounted service contracts Energy-efficient upgrades 10–15% power cost reduction Install variable frequency drives (VFDs) Spare parts inventory 30% faster repairs Stock high-wear items (seals, filters)
- Why Modern Systems Excel
- Adaptability: Handle diverse powders from talc to titanium dioxide.
- Compliance: Meet FDA 21 CFR Part 11 and EU MDR standards.
- Scalability: Upgrade from semi-auto to full automation without replacing core systems.
- Implementation Roadmap
- Audit current workflows to identify bottlenecks
- Phase in upgrades starting with predictive maintenance tools.
- Negotiate lifecycle support with suppliers for parts and train