How much does a chemical raw material packaging machine cost? How to implement scientific corrosion prevention?
Chemical raw material packaging machines are essential in chemical, pharmaceutical, and industrial production, ensuring safe and efficient packaging of corrosive, toxic, or hazardous materials. However, prolonged exposure to aggressive environments can lead to equipment corrosion, affecting performance and safety.
At Yuhang Technology Co., Ltd., we manufacture highly durable chemical packaging machines with anti-corrosion coatings, stainless steel construction, and advanced sealing technology, ensuring long-term reliability in harsh conditions.
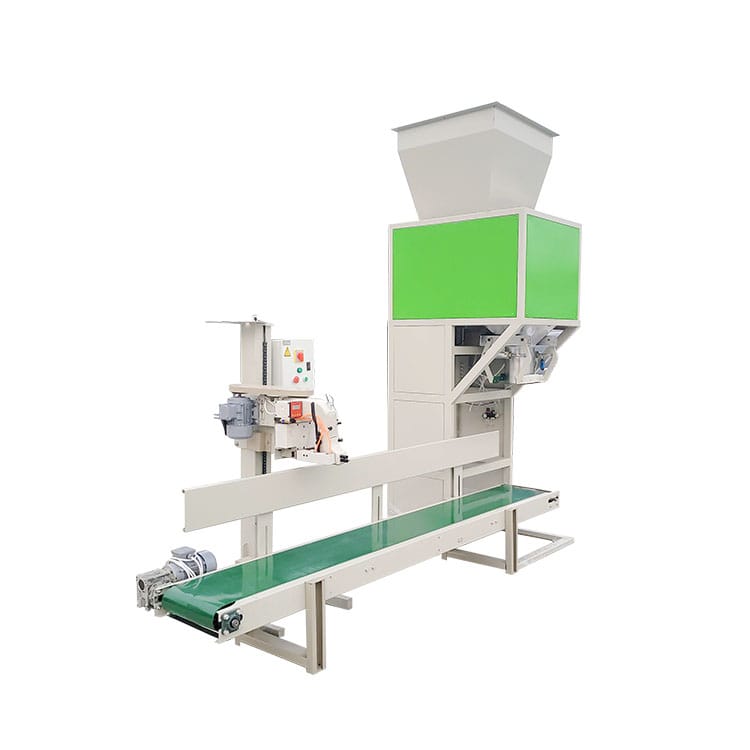
Chemical Raw Material Packaging Machine Price
The cost depends on:
✅ Material Compatibility – Stainless steel (316L for acids), titanium, or coated carbon steel.
✅ Automation Level – Semi-auto ($20,000–$50,000) vs. fully auto ($60,000–$150,000+).
✅ Corrosion Resistance – Special coatings, PTFE linings, or ceramic components.
✅ Safety Features – Explosion-proof motors, gas detection, and leak prevention.
Price Estimates:
- Basic semi-automatic models: $25,000–$60,000
- Fully automated lines: $80,000–$200,000+
For customized corrosion-resistant solutions, contact Yuhang Technology Co., Ltd.—we offer cost-effective, long-lasting packaging systems.
Key Causes of Corrosion in Chemical Packaging Machines
1. Environmental Factors
- Acidic Gases (CO₂, SO₂, H₂S) – React with metal surfaces.
- High Humidity & Temperature – Accelerate oxidation and rust.
- Chemical Spills – Residual acids/alkalis degrade equipment.
2. Material & Design Flaws
- Low-Quality Metals – Prone to pitting and galvanic corrosion.
- Poor Sealing – Allows moisture/chemical infiltration.
- High-Friction Parts – Wear exposes raw metal to corrosion.
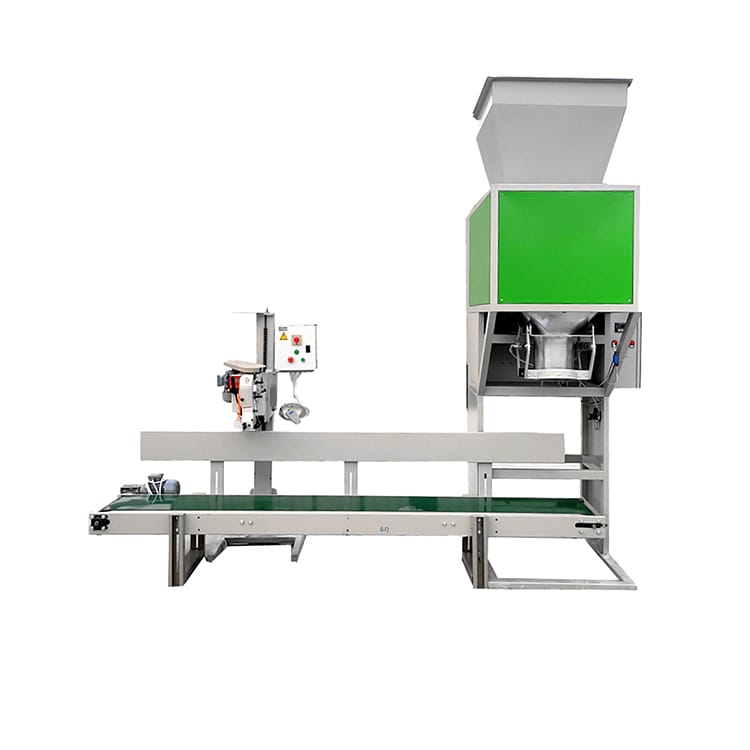
Scientific Anti-Corrosion Measures
1. Material Selection
✔ Stainless Steel (316L/904L) – Resists acids, chlorides, and sulfides.
✔ Titanium Alloys – Ideal for extreme chemical exposure.
✔ PTFE/FEP Linings – Non-reactive plastic coatings for hoppers/seals.
2. Surface Treatment Technologies
- Sandblasting (Abrasive Cleaning) – Removes rust/oxides before coating.
- Thermal Spraying (Aluminum/Zinc) – Forms protective metallic layers.
- Electroplating (Chromium/Nickel) – Enhances hardness & corrosion resistance.
3. Operational Best Practices
- Regular Cleaning – Flush with neutralizers (e.g., sodium bicarbonate for acids).
- Climate Control – Dehumidifiers in packaging areas.
- Routine Inspections – Check for coating damage or seal wear.
4. Advanced Protection Systems
- Cathodic Protection – Sacrificial anodes for underground/marine use.
- VCI (Vapor Corrosion Inhibitors) – Emit protective gases in enclosed spaces.
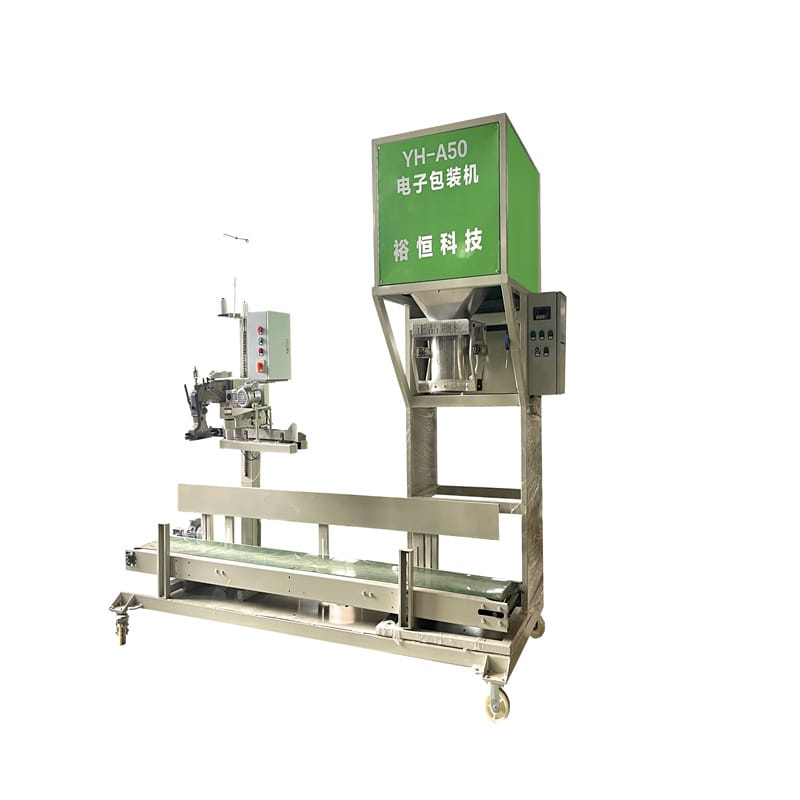
Why Choose Yuhang Technology Co., Ltd.?
✔ Corrosion-Resistant Designs – 316L stainless steel + PTFE options.
✔ Smart Monitoring – Sensors detect leaks/humidity in real time.
✔ Custom Engineering – Tailored for sulfuric acid, caustic soda, solvents, etc.
✔ Low Maintenance – Modular components for easy part replacement.
Conclusion
Investing in a high-quality chemical raw material packaging machine with anti-corrosion features minimizes downtime and safety risks. Prices vary based on materials, automation, and protection systems.
For durable, chemically resistant packaging solutions, trust Yuhang Technology Co., Ltd.—contact us today for a consultation!