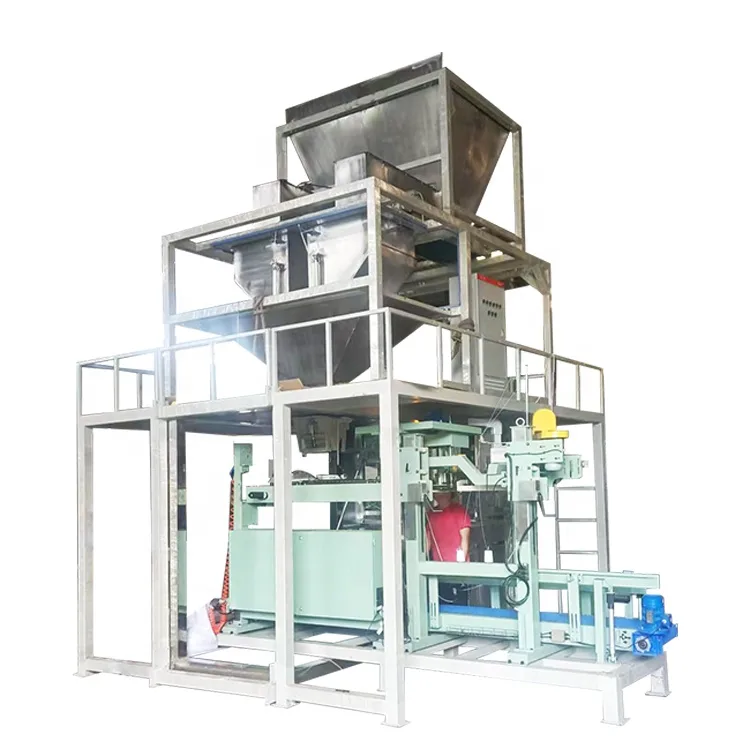
Automatic particle packaging machine how much a? What should it pay attention to in the work?
I. Price Analysis of Automatic Granule Packaging Machines
The price of automatic granule packaging machines is influenced by factors such as brand, model, functional configuration, degree of automation, and production capacity. The mainstream price range in the 2024 market is as follows:
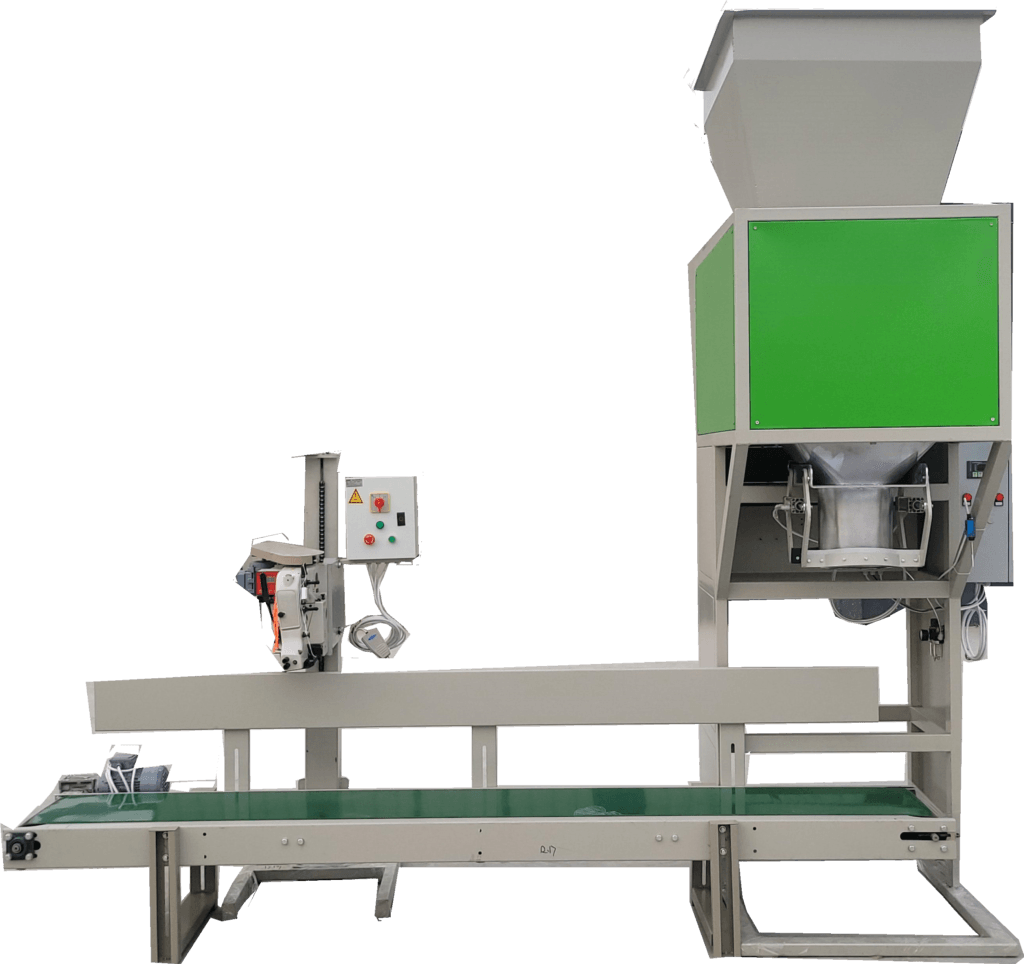
- Economical Semi-automatic Models: 1300 – 4200USD
- Suitable for small enterprises or start-up factories, requiring manual assistance for bagging and sealing. The packaging speed is approximately 200 – 300 bags per hour.
- Representative models: Basic single-scale measurement models, suitable for small-scale production with a daily output of less than 2 tons.
- Mid-range Fully Automatic Model: 4200 – 11000USD
- Integrated with automatic weighing, bag-making and sealing functions, capable of switching to multiple specifications, with packaging accuracy of ±0.2%, and speed ranging from 400 to 600 bags per hour.
- Typical configuration: For instance, the Shanghai Zhuheng 15-30kg model, suitable for medium-sized enterprises with daily production capacity of 10-20 tons.
- High-end Intelligent Models: 11000 – 21000 USD
- Equipped with IoT monitoring, dual-scale parallel operation, dust removal system, the packaging speed can reach 800 – 1,000 bags per hour, and supports remote operation and maintenance.
- For instance, the XFG-K bag-injection type fully automatic model is suitable for granular packaging of products like extruded foods and dried fruits, with a packaging capacity of 30 – 50 bags per minute.
Key Factors Affecting Prices:
- Automation Degree: The price of fully automatic equipment is 2-3 times that of semi-automatic ones;
- Functional Modules: Additional features such as the material of the heat sealing knife (ordinary steel/ceramic), dust removal system, and intelligent control screen increase the cost;
- Brand Premium: Well-known brands (such as Hengwei, Bangdeluo) have a price increase of 10%-20%, but they offer more reliable after-sales service.
2. Safety Operating and Maintenance Precautions
(I) Pre-Startup Inspection
- Equipment Environment: Clear the area within 1 meter around the machine of any debris. Check the tension of the drive belt (flexibility of 10-15mm), and ensure the oil level of the lubrication system is at the midline of the sight glass.
- Power Supply and Protection: Confirm that the emergency stop button is not locked, that the grounding wire connection is reliable, and that the protective cover is intact and undamaged.
(II) Operating Specifications
- Safety Distances:
- Prohibit any part of the body from approaching the sealing roller with a rotational speed of 120 revolutions per minute or the cutting knife assembly operating at a frequency of 2 times per second. Maintain a safety distance of at least 50 cm.
- Do not place tools within 1 meter of the vibration table to avoid the risk of being caught up.
- Operational Permissions:
- Each device is restricted to one operator. For collaborative operations involving multiple people, switch to the collaborative mode (button response delay: 0.5 seconds) to prevent accidental touches.
- Parameter Management:
- It is prohibited to frequently switch buttons or modify parameters (such as temperature and speed) to prevent system disorder. Any parameter changes should be recorded with the operator’s name, the time of the operation, and the basis for the change, and the records should be kept for at least 3 years.
(III) Maintenance and Emergency Response
- Power Failure Maintenance:
- During maintenance, the “Tag and lock” (Tag means “Warning sign” or “signing a notice”, and Lock up means “locking”) procedure must be followed: Hang a red warning sign, lock the power box with a dedicated lock, and keep the key with the person in charge.
- Regular Maintenance:
- Lubricate bearings, gears and other components monthly. For the first oil change of the reducer, it should be done after 10 days of operation. Subsequent oil changes should be conducted every 2,000 hours. When cleaning the heat sealing device, use a copper brush. Do not operate it by hand.
- Fault Handling:
- In case of abnormal conditions (such as frequent abnormal noises from bearings or surface temperature exceeding 60℃), execute the third-level shutdown immediately: activate the warning light → slow down → cut off power supply. In the event of abnormality in the sealing knife zone, the equipment can forcibly retract within 0.08 seconds, but manual intervention is still required.
(IV) Environmental and Personnel Management
- Workshop Environment: The humidity should be kept below 90%. For environments with high temperature and high humidity, moisture-proof electrical components need to be selected.
- Personnel Training: Operators must pass safety assessments and be familiar with the equipment structure and emergency response plans. They should wear dust-proof masks and cut-resistant gloves.
III. Suggestions for Purchase and Usage
- Test Machine: Test the compatibility of the bagging device with common packaging bags by carrying out continuous packaging of 100 bags to check the error rate;
- Cost Control: Choose manufacturers that offer 1-year warranty and free debugging services. Compare energy consumption (the fully automatic model consumes 3-5 kWh per hour);
- Post-Sales Evaluation: Prioritize brands that have service stations in major production areas (such as Henan and Shandong) to ensure a 48-hour emergency response.
For specific model quotations or operation manuals, you can refer to the manufacturer information on webpages 1, 3, 7 and 9, or filter suppliers through Alibaba platform to obtain detailed parameters.
If you want to know more about the equipment configuration and other details, please feel free to communicate with us