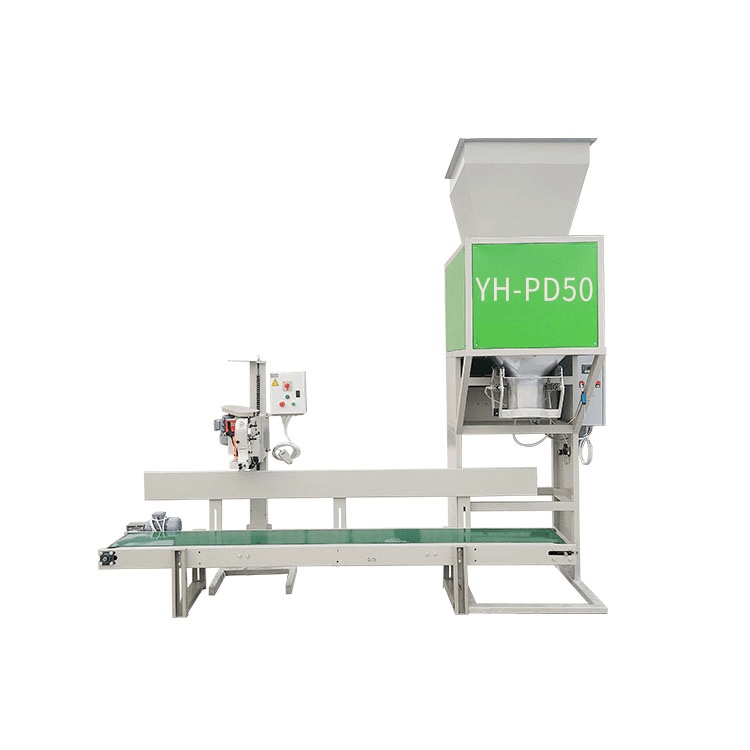
How Much Does a Cereal Packaging Machine Cost? 6 Key Benefits Transforming Oatmeal Production
Cereal packaging machines have become indispensable in the competitive food processing industry, enabling manufacturers to optimize efficiency while maintaining product quality. YU-HENG Technology, a leader in packaging innovation, leverages China’s advanced manufacturing ecosystem to deliver cost-effective, high-performance solutions for global clients. This article analyzes cereal packaging machine pricing and their transformative advantages, with a focus on operational ROI and technical excellence.
Cereal Packaging Machine Pricing & Cost Advantages
YU-HENG Technology offers tiered solutions to match diverse production needs:
- Semi-automatic models: $5,000–$60,000, ideal for SMEs, outputting 800–1,200 bags/hour (13–20 bags/minute).
- Fully automated systems: $80,000–$140,000, integrating weighing, filling, and sealing functions at 150 bags/minute (±0.5 oz/14g accuracy).
- Customized lines: $200,000+, supporting multi-blend packaging (e.g., oats with nuts/dried fruits) and IoT-enabled management.
Chinese-manufactured machines provide 25–40% cost savings versus European/North American equivalents, with 50% lower spare parts costs. YU-HENG’s modular designs shorten delivery lead times to 4–6 weeks, backed by a 3-year comprehensive warranty.
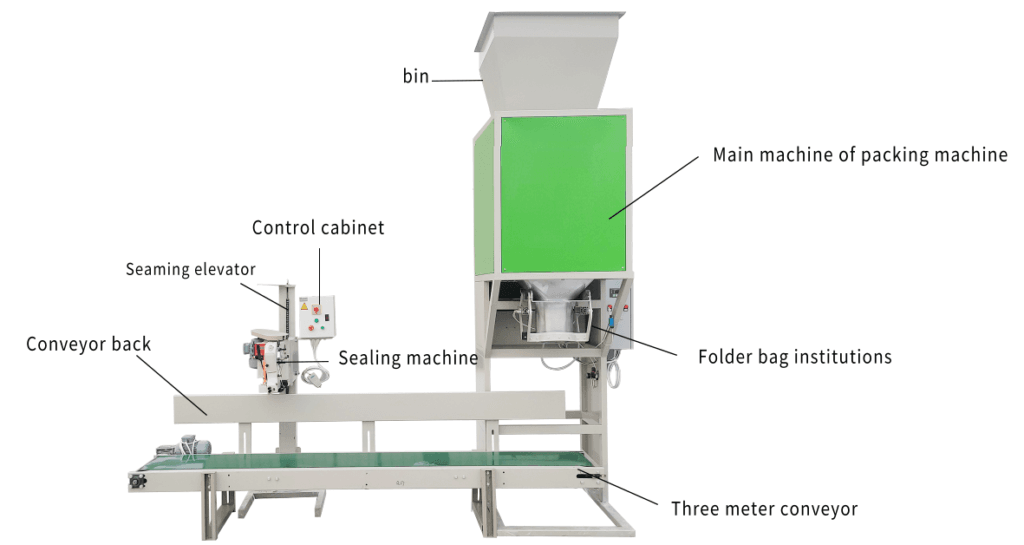
6 Operational Benefits of Modern Cereal Packers
1. Productivity Revolution
Automated systems replace 8–10 manual workers, boosting output by 500%. The YU-HENG HX-360 model exemplifies this leap:
- Servo-driven mechanisms handle flakes, granules, and mixed textures
- Real-time monitoring of temperature (200–450°F/93–232°C) and pressure (10–15 PSI)
- Annual downtime reduced to <0.1% via predictive maintenance alerts
2. Labor Cost Optimization
Clients report $150K–$250K annual savings in labor expenses. YU-HENG’s intuitive touchscreens feature:
- Multilingual interfaces (English/Spanish/French)
- One-click format changes between bag styles
- Operator training shortened from 2 weeks to 3 days
3. Quality Assurance & Shelf Life Extension
YU-HENG’s nitrogen flushing technology maintains <0.5% oxygen levels, while ultrasonic sealing ensures:
- 30–50% longer shelf life versus conventional packaging
- <0.03% damage rate during shipping (third-party verified)
- Compliance with FDA 21 CFR Part 177 food contact standards
4. Brand Differentiation
Enhance market appeal through:
- 12 customizable bag formats (stand-up pouches, family-size boxes)
- HD printing at 1200 dpi with 98% Pantone color matching
- Tamper-evident features like laser-perforated tear strips
5. Market Agility
Adapt quickly to consumer trends:
- Adjust portion sizes from 1.1–4.4 lb (0.5–2 kg) in <10 minutes
- Handle organic oats, high-protein granola, and gluten-free blends
- Small-batch production capability (500+ units)
6. Sustainability & Energy Efficiency
YU-HENG’s eco-design reduces:
- Energy consumption by 25% via self-regulating heat seals
- Film waste by 15% through edge trim recycling systems
- Carbon footprint with solar-ready configurations
YU-HENG Technology’s Competitive Edge
- Patented Innovations: Moisture-proof metering chamber (Patent ZL2022XXXXXX), low-friction film feed system
- Global Support: 8 technical centers across Americas/EMEA/APAC, 48-hour emergency response
- Smart Manufacturing: YH-Cloud platform boosts OEE (Overall Equipment Effectiveness) by 18% through real-time analytics