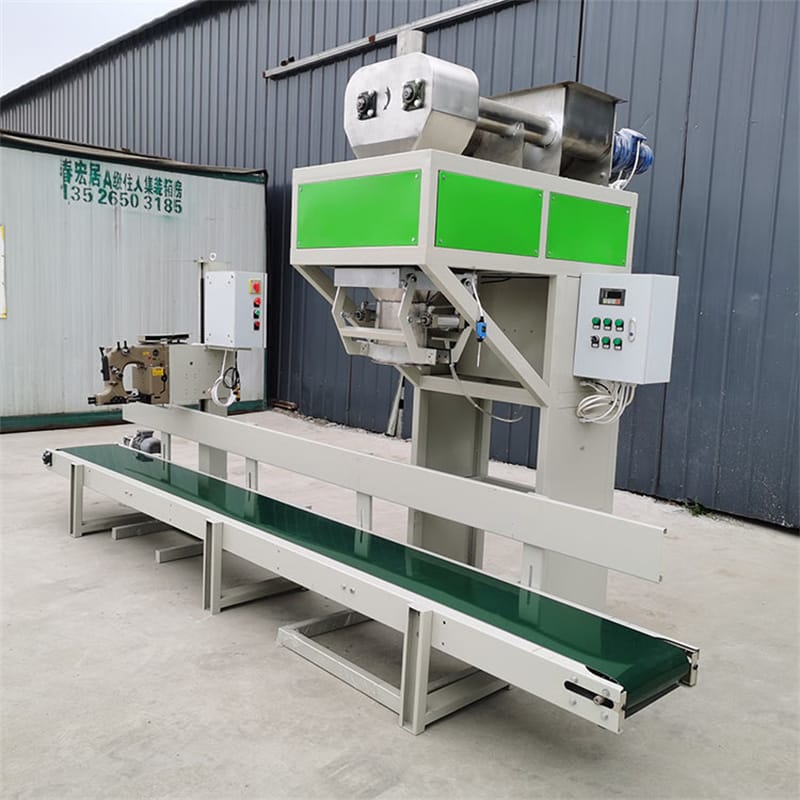
How Much Does an Automatic Powder Packaging Machine Cost? Key Factors and Troubleshooting Solutions
The automatic powder packaging machine has become indispensable in industries like food, pharmaceuticals, and chemicals due to its precision and efficiency. However, selecting the right equipment and addressing operational challenges require careful consideration. This comprehensive guide covers pricing structures and proven solutions for common malfunctions.
Pricing Structure and Key Determinants
Automatic powder packaging machines typically range from $15,000 for basic semi-automatic models to over $100,000 for high-speed, fully automated systems with advanced features. Several critical factors influence the final investment: production capacity (measured in bags per minute), construction materials (food-grade stainless steel commands a 20-30% premium), weighing accuracy (commercial standards require ±0.1-1% tolerance), and additional functionalities like integrated dust extraction or clean-in-place systems. Notably, branded equipment from manufacturers like Bosch or Siemens carries significant price premiums due to their established reliability and comprehensive service networks.
Operational Challenges and Technical Solutions
Material feeding issues rank among the most frequent operational problems. When the hopper runs empty due to inadequate monitoring, it triggers production stoppages and measurement inaccuracies. Modern solutions incorporate automated screw conveyors with ultrasonic level sensors and intermediate buffer silos sized at 150% of batch volume to ensure continuous operation. For powders with cohesive properties, daily maintenance protocols should include compressed air purging of all contact surfaces, complemented by weekly ultrasonic cleaning of disassembled components using food-safe solvents. Sticky materials often require equipment modifications such as heated hoppers (maintained at 40-60°C) or specialized twin-screw configurations with anti-bridging designs to prevent clogging.
Precision Calibration and Maintenance Protocols
Achieving consistent measurement accuracy demands regular equipment calibration. Monthly verification of load cells should maintain deviations within ±0.5% of target weights, with particular attention to screw wear – any clearance exceeding 0.5mm between the screw and housing necessitates immediate replacement. Pneumatic systems require periodic pressure verification (0.2-0.5MPa range) to ensure proper material fluidization. For operations handling hygroscopic powders, environmental controls maintaining relative humidity below 45% significantly reduce material clumping and associated downtime.
Advanced Monitoring and Cost Optimization
Progressive operations now implement IoT-enabled predictive maintenance systems that analyze vibration patterns, motor current fluctuations, and thermal imaging data to forecast 80% of potential failures 72 hours in advance. While requiring an initial investment of $3,000-$5,000 annually, these systems reduce unplanned downtime by 85% compared to traditional reactive maintenance approaches. For facilities operating multiple packaging lines, centralized monitoring stations provide real-time alerts and historical performance analytics, enabling data-driven decisions about equipment upgrades or replacement cycles.
Conclusion and Recommendations
Selecting an automatic powder packaging machine involves balancing capital expenditure against operational requirements, with particular attention to material characteristics and production volumes. Implementing structured maintenance routines and investing in monitoring technology typically yields a 12-18 month return on investment through reduced downtime and material waste. For operations handling specialty powders (explosive, corrosive, or ultra-fine nanomaterials), consultation with packaging engineers is strongly advised to specify appropriate containment and safety features.
If you want to know more about the equipment configuration and other details, please feel free to communicate with us