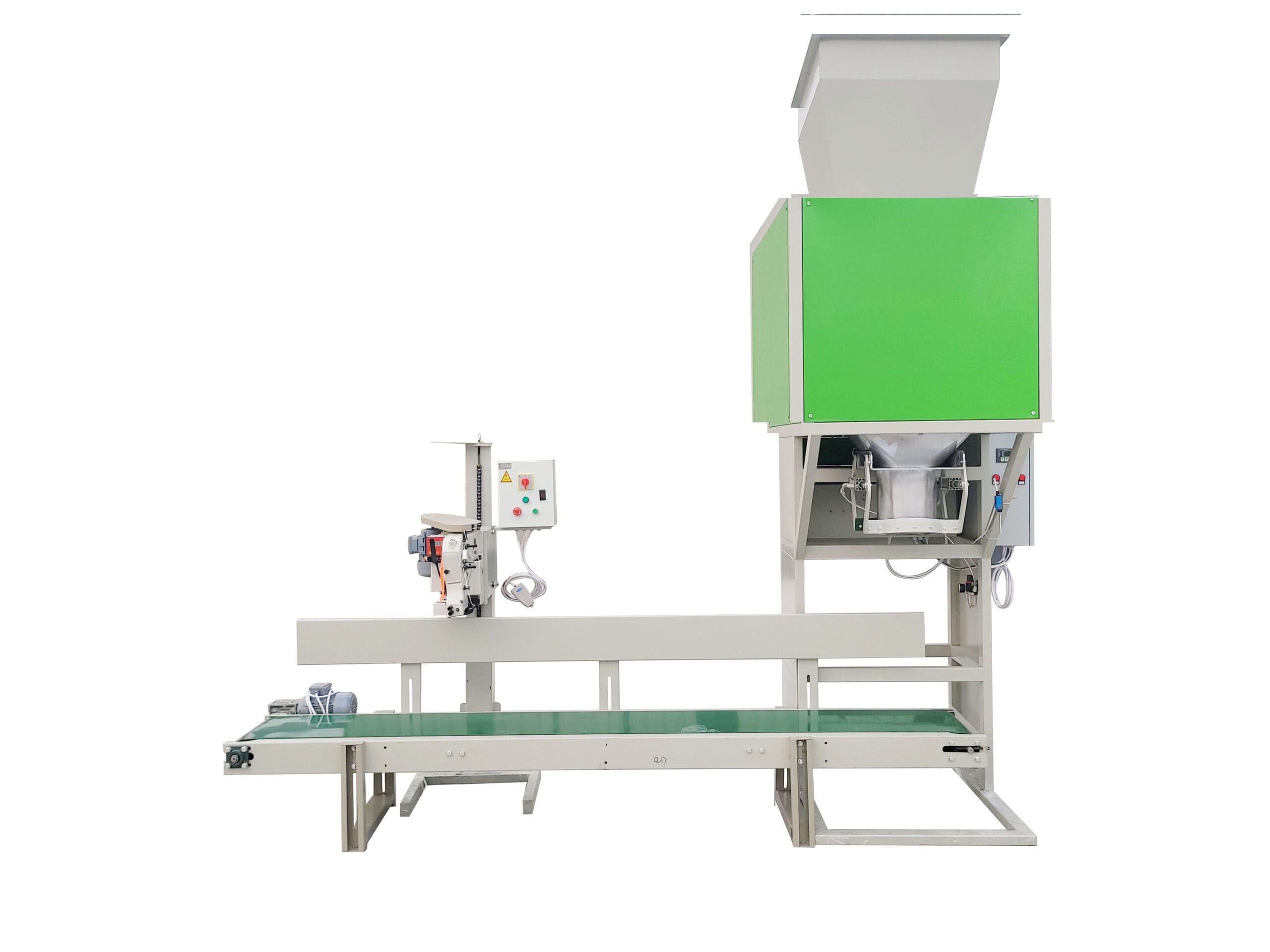
25kg Automatic Packaging Scale Costs & Step-by-Step Commissioning Guide
For industries handling bulk materials like fertilizers, grains, or chemicals, 25kg automatic packaging scales are essential for efficient operations. Below, we break down pricing factors and provide a systematic commissioning protocol to ensure precision and reliability.
25kg Automatic Packaging Scale Pricing
Equipment costs depend on accuracy and automation features:
- Basic models: $25,000–$40,000 (±0.5–1% accuracy)
- Mid-range systems: $45,000–$75,000 (±0.3–0.5% accuracy, IoT-ready)
- High-precision models: $80,000+ (±0.1–0.2% accuracy, GMP-compliant)
Chinese manufacturers like YU-HENG Technology offer 30–40% cost savings versus European brands while maintaining ISO 9001-certified quality.
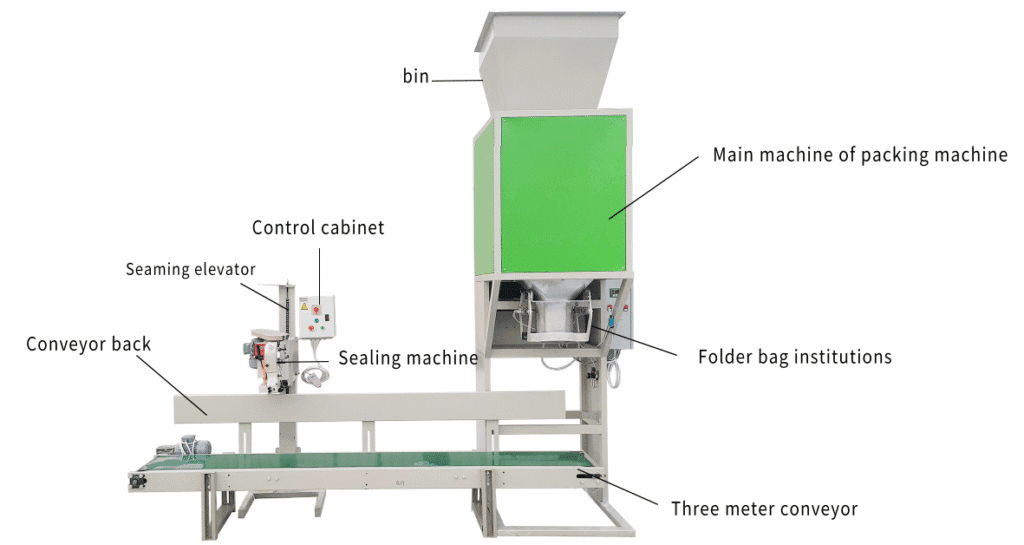
6-Step Commissioning Protocol
1. Post-Installation Verification
- Checklist:
- Confirm structural alignment per blueprints (tolerance <0.04″/1mm).
- Inspect electrical/pneumatic connections for leaks or loose terminals.
- Verify hopper and conveyor belt clearance (≥2″/50mm from walls).
Pro Tip: Use laser alignment tools for rapid verification.
2. Parameter Initialization
- Critical Settings:
Parameter Typical Range
Target weight 55.1 lb (25 kg ±0.5%)
Feed speed 3–6 seconds/bag
Overfill prevention 1–2% buffer adjustment Example: For hygroscopic materials like powdered milk, reduce feed speed by 20% to prevent bridging. 3. Photoelectric Sensor Calibration- Testing Method:Place a 55 lb (25 kg) test bag in the detection zone.Verify sensor triggers “bag present” signal within 0.1 seconds.Test empty zone detection (no false positives after bag removal).
- Empty Run (30 mins):Monitor motor temperature (<140°F/60°C).Check for abnormal vibrations (>2 mm/s requires rebalancing).Loaded Run (10 cycles):Weigh 10 bags post-filling using calibrated bench scales.Acceptable deviation: ≤±0.35 lb (±0.16 kg) for 55 lb (25 kg) bags.
- Functional Checks:Auto-stop on overweight (e.g., 56.4 lb/25.6 kg triggers alarm).Sequential operation (bag placement → filling → sealing → ejection).Data logging accuracy (time stamps ±1 second).
- 6. Mechanical Fine-Tuning
- Key Adjustments:Feed gate: Optimize opening/closing timing to ±0.2 seconds.
- Auger clearance: Maintain 0.08–0.12″ (2–3 mm) gap for free-flowing powders.
- Bag clamp pressure: 15–25 PSI (1–1.7 bar) to prevent slippage.
- Daily Checks:Lubricate linear guides with ISO VG 32 oil.Clear residual material from load cells.
- Monthly Maintenance:Recalibrate scales using certified 55 lb (25 kg) test weights.Inspect wear parts (auger flights, seal jaws).
- Annual Overhaul:Replace worn bearings and belts.Validate compliance with NTEP/NIST standards.
- Troubleshooting Common Issues Symptom Likely Cause Solution
- Inconsistent filling Material bridging Install vibrators or air assists Weight drift over time Temperature fluctuations Enable thermal compensation False sensor triggers Dust accumulation Upgrade to IP69K-rated sensors
- Why Choose Chinese-Made Systems?
- Fast ROI: Most users recover costs in 12–18 months via labor savings.
- Customization: Adapt auger designs for sticky or abrasive materials.
- Support: 24/7 multilingual technical assistance with 48-hour response.